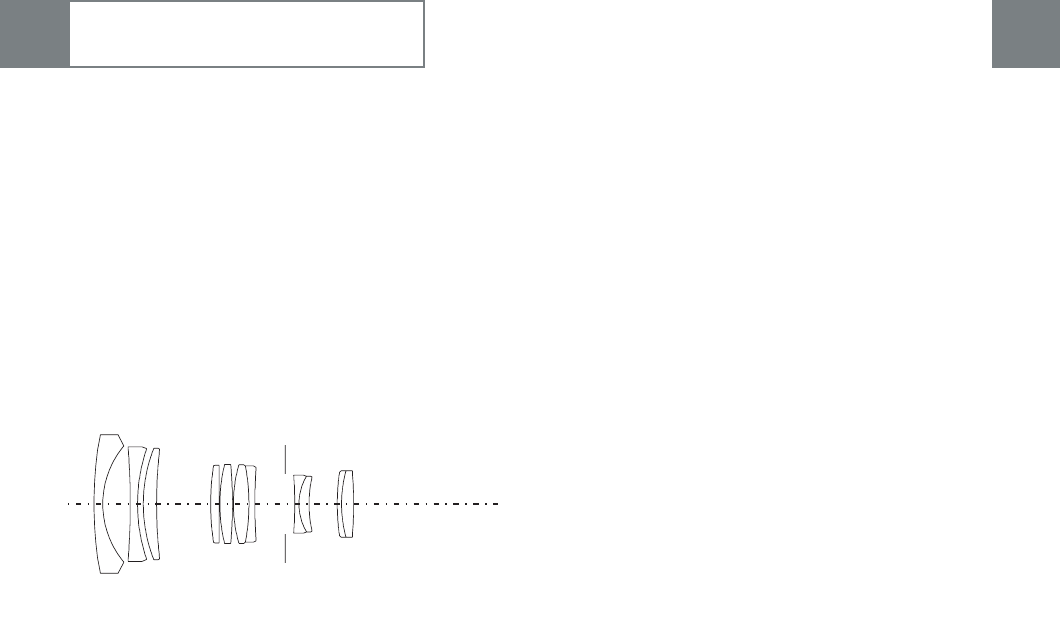
Chapter 7 Leica R-Lenses 3
__Optical demands and mechanical con-
struction
The design has 11 elements in 8 groups and employs two
aspherical surfaces, one at the first surface of the front ele-
ment and one at the second surface of the last element,
incidentally the same as in the original Noctilux 50 mm
f/1.2.
The lens has three moving groups that are being guided in
milled slots with a precision of 0.010 to 0.005 mm.
The challenge for the Leica engineers was to design a lens
that had to fit into three dimensions of requirements: per-
formance, haptics and cosmetics. These dimensions are
partly at conflict with each other. And we have to add anot-
her dimension, that is the manufacture of the lens. In this
area Leica has learned a lot from the previous designs. The
main problem area is the narrow tolerance band for the
manufacture and assembly. The lens consists of eleven lens
elements, that are precision grinded and have a surface tre-
atment to reduce surface irregularities to a sub micron
level, in fact here we are talking about tolerances at the
nanometer scale (0.001 micron). To deliver the required and
calculated performance, the lens element must be fitted
into the mount without any stress, as the slightest strain on
the lens will deform the surface and produce unwanted
optical aberrations. One should be aware that the accurate
and strain free mounting of the lens elements is a big chal-
lenge. There are additional challenges too: a lens element
needs to be blackened at the sides to reduce the possibility
of flare. This is accomplished by painting the sides of the
lens with a black paint, still done by hand by experienced
workers. But a thick (relatively speaking!) elastic layer
implies that the lens could move ever so slightly within the
mount. One solution might be to press the glass element
into its mount, but too much pressure is not good at all. So
one has to carefully balance the thickness of the layer of
paint with the requirement of a strain free fitting.
In the area of lens grinding and shaping we are operating
on a nanometer dimension. The jump from this optical
dimension to the mechanical dimension of the mount and
the accuracy of assembly is a jump from nanometer scale
to micrometer scale (0.001 mm), but this micrometer scale
is still incredibly small. And the designer must be aware of
this jump to assure that his calculations can be met in the
realm of manual assembly, even when using sophisticated
instruments to check the precision of the assembly. The
new zoomlens has more than 40 main mechanical parts
(excluding the elements and electronics and the aperture
mechanism) that have to be assembled with a precision of
0.010 to 0.005 mm.
One of the biggest problem areas in lens assembly is the
possible decentring of lens elements. Decentring of lens
elements can be a tilt or a lateral displacement (relative to
the optical axis) and will occur almost always during lens
assembly unless one can work with very narrow tolerances.
Most optical programs have a special module to study the
effects of decentring and can indicate how much decen-
tring is allowable before one sees a deterioration of the
image quality.
Decentring in general brings loss of contrast and more
astigmatism. A special construction is required to ensure
that the very tight tolerances that this lens demand (due to
the mechanical and optical constraints of a 1:3 zoomrange).
The manufacture of parts can never be done in a zero-tole-
rance environment. Therefore a certain amount of tolerance
in the system must be accepted. In general one can appro-
ach this problem in three ways: one can allow for adjust-
ments during the assembly process and try to pair
plus/minus parts to get the correct fit (old Leitz method),
one can do a Monte Carlo statistical analysis to investigate
where the most sensitive problem areas are and distribute
the problematic aspect through the system by relaxing the
constraint (Zeiss method of relaxation) and now Leica uses
a third method. This is the method of mechanical compen-
sators that are part of the mechanical construction and are
already taken into account at the stage of optical design
and calculation. This is the novel idea. Compensators them-
selves are not new as a technique. In this case the lens ele-
ment can be displaced by a small amount by a mechanical
movement before being fixed in place. The displacement is
controlled by a MTF measurement at a very high scale of
magnification
New too is the approach to design the lens optically and
mechanically at the same time and in full interaction. The
designer must be aware what is possible at the assembly
stage as he cannot demand the impossible from the people
during their work. The optical calculations are optimized to