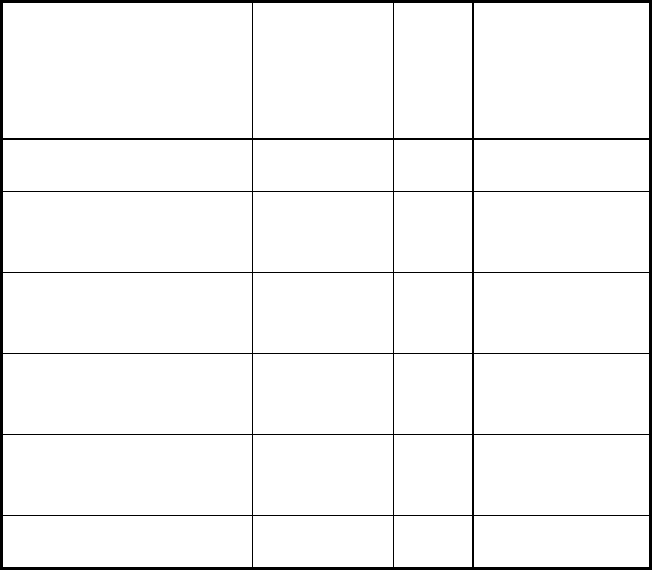
Data Sheet—3 Copyright, Eastman Kodak Company, 1999
TI2497 Issued 11-99
Notice: Observe precautionary information on product labels and on the Material Safety Data
Sheets.
Processing Step Temperatu
re
Time
Replenishment
Rate
(mL per 100
ft)
35 mm
KODAK Developer D-
97
[1]
70°F (21°C)
—
[2]
650
(D-97R)
Stop Rinse
[3]
70°F (21°C)
50
sec
12,000
KODAK Fixing Bath
F-5
[1]
70°F (21°C)
6 min
600
Wash (counter-
current)
70°F (21°C)
10
min
12,000
Dry 95 °F(35 C) —
[4]
[1]
Agitation in the developer and fixing bath should be by recirculation through submerged spray
jets that impinge on the film strands.
[2]
Develop to recommended control gamma of 2.4 to 2.6 (Status A). Calculation to obtain control
gamma is Dmin + 0.95 density to + 0.50 log E.
[3]
Countercurrent flow of fixer-laden water overflow from the wash tank, pH about 6.
[4]
Many factors affect the drying: air temperature, relative humidity (RH); volume, rate and
distribution of the airflow; final squeegeeing, etc.
SO-302 has a slightly higher wet load. Since processor dryer conditions vary, please monitor the film as it goes
through the dryer the first time to assure that the film is being adequately dried. Adjust drier accordingly.
In a conventional convection-type drying cabinet with air at about 95°F (35°C) and 40 to 50 percent RH, drying will
take 15 to 20 minutes. With an impingement type drying cabinet (with a higher temperature and lower RH), drying
time is greatly reduced. With either type of dryer, the film should be dry without tackiness 1/2 to 2/3 of the way
through. Upon cooling to room temperature after leaving the dryer, the film should be in equilibrium with the room air
at approximately 50 percent RH.
Print film occasionally exhibits "static cling" during projection, where several laps of the film may stick together as they
feed to the control arm on a platter, causing erratic platter behavior and possible film jam or "brain wrap". This behavior
is affected by the design of the platter, the ambient conditions in the projection room, the winding orientation and curl
of the film, and a variety of other factors. Kodak recommends maintaining a relative humidity of 50-60 percent RH in
the projection room.
Staticide 3000G, a process additive available from ACL Staticide, may be added to the final wash (tank and replenisher)
of the D97 Process at a concentration of 0.01% (0.1 ml per liter) to reduce the incidence of "static cling". Kodak testing
and trade experience have shown that films having a process-surviving conductive anti-static backings will be much less