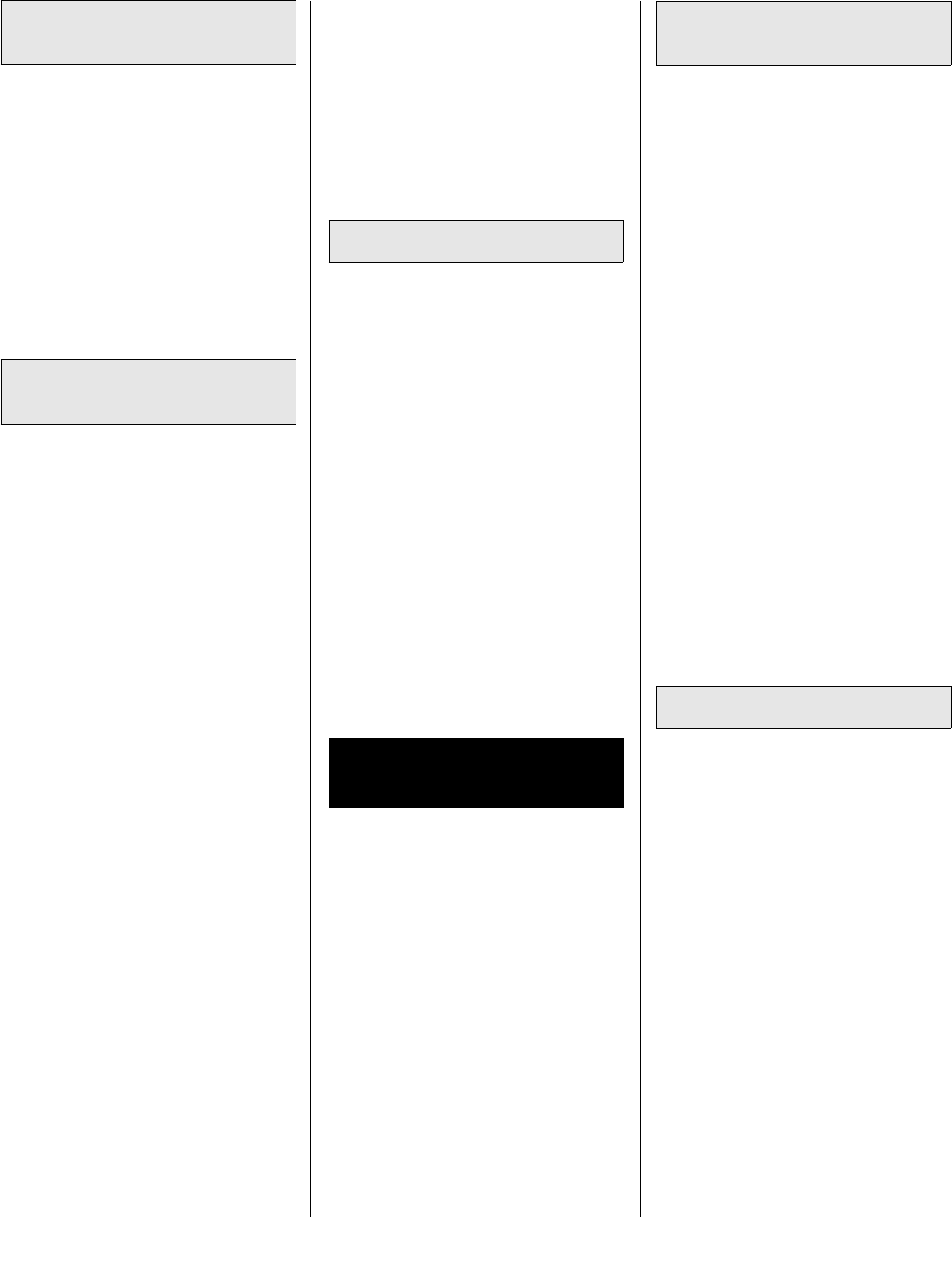
Safe Handling of Photographic Processing Chemicals • J-98A2
OSHA requires that personal
protective equipment (PPE) be used
in the workplace whenever the
possibility of chemical contact
exists. OSHA also requires that you
perform a hazard assessment in
your facility to determine what type
of PPE is required to protect against
the hazards present. In general, the
PPE required for handling
photographic processing chemicals
includes:
• Neoprene or nitrile gloves
• Safety goggles
• Vinyl rubber apron or lab coat
Check personal protective
equipment often to make sure it is in
good working condition, clean, and
works and fits properly. Training
must be provided on the use,
limitations, maintenance, and how
to wear PPE. For more information,
see KODAK Publication No. J-312,
Personal Protective Equipment
Requirements for Photographic
Processing Facilities.
Certain photographic processing
chemicals contain materials that can
burn or irritate the skin and eyes,
sometimes with only brief contact.
To reduce the possibility of injury,
always wear personal protective
equipment when handling
photographic processing chemicals.
Also make sure an emergency eye
wash station is readily available.
PERSONAL PROTECTIVE
EQUIPMENT
CORROSIVE MATERIALS
The Occupational Safety and Health
Administration (OSHA) Hazard
Communication Standard requires
chemical manufacturers to provide
Material Safety Data Sheets (MSDSs)
for hazardous chemicals. OSHA also
requires employers to make MSDSs
available in the workplace for the
purpose of proper chemical
container labeling, and training
employees on the safe use of
chemicals.
Photographic processing facilities
are required by OSHA to have
MSDSs for all hazardous chemicals.
MSDSs provide detailed
information about each product.
Information included in MSDSs is
outlined in the following categories:
• chemical and manufacturer
identification
• composition/ingredients
• hazard identification
• first-aid measures
• fire-fighting measures
• accidental release measures
• handling and storage
• exposure controls and personal
protection
• physical and chemical properties
• stability and reactivity
• toxicological issues
• ecological issues
• disposal issues
• transport issues
• regulatory issues, and other
information.
YOUR LAB’S HEALTH AND
SAFETY PROGRAM
MATERIAL SAFETY DATA
SHEETS
Kodak provides customers with
MSDSs for all photographic
processing chemicals. If you need
replacement(s) or extra MSDSs for
any Kodak chemical, call 1-800-242-
2424, extension 43. You will need to
supply the catalog (CAT) number of
the products for which you need
MSDSs.
OSHA requires that all employees
be trained on the safe handling of
photographic processing chemicals
and general lab safety prior to their
initial assignment and whenever
new hazards are introduced into the
workplace. Employees should be
familiar with the OSHA Hazard
Communication Standard,
operations where hazardous
chemicals are present, the location
and content of Material Safety Data
Sheets, physical and health hazards
of chemicals in their work area, as
well as additional topics. For more
information on OSHA’s Hazard
Communication Standard, see
KODAK Publication No. J-311,
Hazard Communication for
Photographic Processing Facilities.
Once you know the hazards, learn
how to handle chemicals safely. Safe
handling practices include wearing
personal protective equipment,
following procedures that minimize
chemical contact, and following the
instructions on chemical labels. If
contact occurs, know how to treat or
obtain medical/first-aid assistance.
TRAINING
HANDLE CHEMICALS
PROPERLY