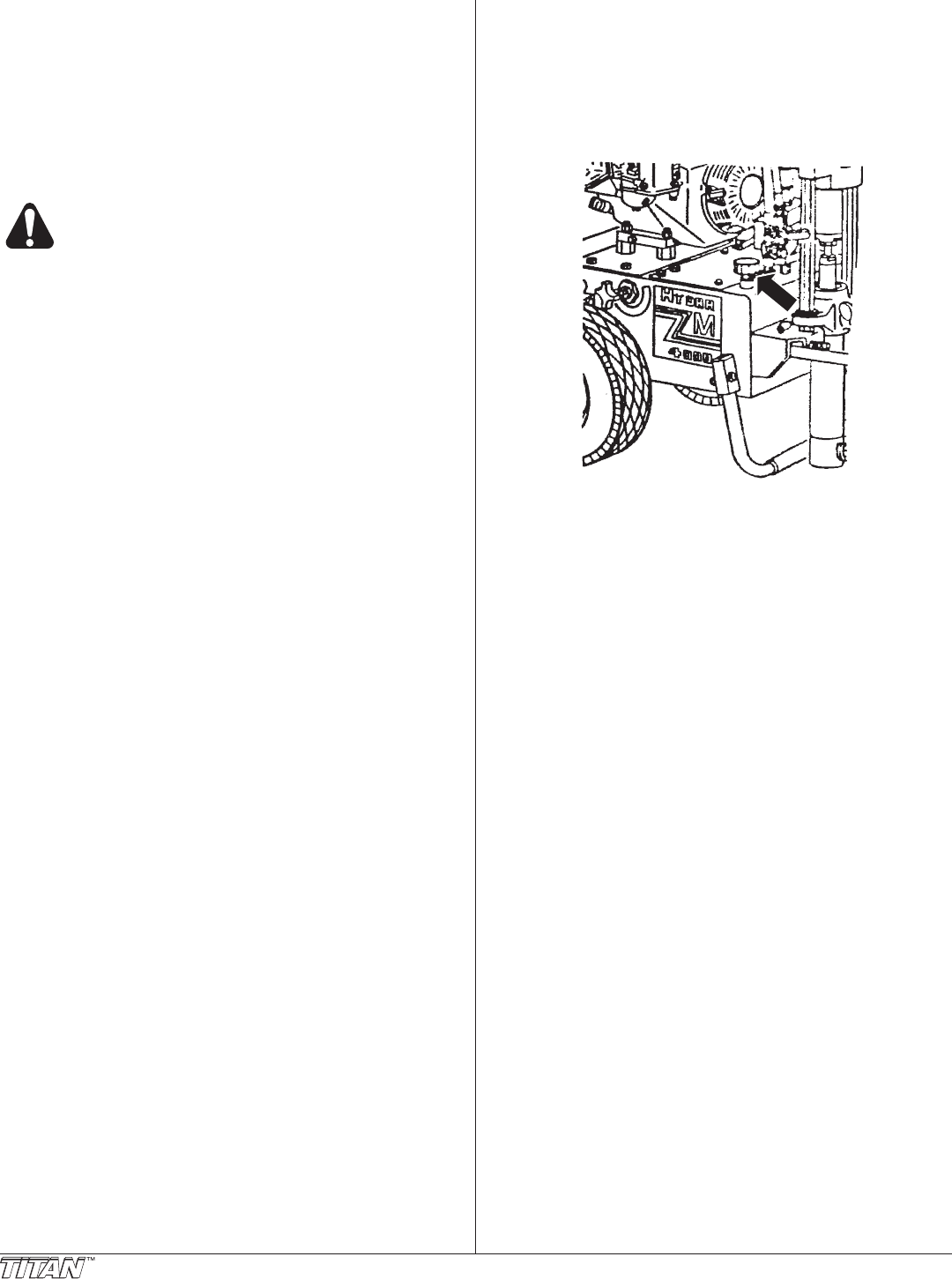
10 © Titan Tool Inc. All rights reserved.
Cleaning a Clogged Tip
1. Follow the Pressure Relief Procedure, page 9.
2. Lock the gun trigger.
3. Unthread the safety tip guard and remove the spray tip.
Wash the tip in solvent and use a tip probe to remove any
clogged material.
4. Release the gun trigger lock and spray briey into a waste
container to blow out any clogged particles.
5. Reset the trigger lock in the “Trigger Locked” position.
Release the trigger lock and resume spraying.
The flow from the spray tip is at very high pressure.
Contact with any body part may be dangerous. Do
not place finger on gun outlet. Do not point the
gun at any person. Never operate the spray gun
without the proper tip guard.
Color Change / Clean Out
IMPORTANT: Use only compatible solvents when cleaning
out oil based enamels, lacquers, coal tar, and epoxies.
Check with the fluid manufacturer for a recommended
solvent.
1. Reduce pressure by turning the pressure adjustment
knob and the pressure bleed valve on the bleed line
counterclockwise. Follow the Pressure Relief Procedure,
page 9.
The pressure bleed valve should be turned counter-
clockwise three full turns.
2. Pull the siphon tube out of the material container.
3. Remove the spray tip from the gun. Hold the gun trigger
open until material ow stops.
4. Put siphon tube into wash solvent or water as applicable,
and operate pump slowly at low pressure until solvent
ows freely from pressure bleed valve line.
5. Close pressure bleed valve and hold gun trigger open
until solvent ows freely from gun. If solvent is not too
dirty, recirculate it by owing gun stream back into solvent
container. Use additional clean solvent and repeat
procedure if necessary.
6. Check gun strainer screen and pump outlet lter screen
daily. Use 50 mesh screens with spray tip size .017 and
larger. Use 100 or 200 mesh screens with spray tip sizes
.015 and smaller.
7. Replace paint lter cap to maximize clockwise rotation.
The lter cover should be hand removable after the rst or
second use with new Telfon O-ring.
IMPORTANT: O-ring must have PTFE backup washer to seal
properly.
8. If unit has been spraying a water soluble material, ush
with water and then repeat procedure with mineral spirits
or Varsol solvent.
9. Wash spray tip in solvent. Blow tip clean with air pressure
directed through the tip in the reverse direction.
Maintenance
Hydraulic System
1. Check the hydraulic uid daily. It should read “Full” on
the dipstick. If it is low, add only Titan Coolo, part #
430-361. Never add or change hydraulic uid except in
a clean, dust-free environment. Contamination of the
hydraulic uid will shorten hydraulic pump life and may
void warranty.
2. Change the hydraulic uid every six months. Drain old
uid from tank and ll with 5 gallons of Coolo. Start
operation of the system at just enough pressure to operate
the uid pump. Run the system at this low pressure for
at least 10 minutes. This removes air from the system.
Check the uid level after this procedure.
3. The hydraulic system has an external replaceable
hydraulic lter. Change the lter every six months.
4. The hydraulic pump should not be serviced in the eld.
If service on the hydraulic pump is required, it must be
returned to Titan.
General Fluid Pump Maintenance
If the paint pump is going to be out of service for an extended
period of time, it is recommended that following cleanup a
kerosene and oil mixture be introduced as a preservative.
Packings may tend to dry out from lack of use. This is
particularly true of the upper packing set for which upper packing
lubricant, Piston Lube, Titan part # 314-480, is recommended
in normal usage. A sample of Piston Lube accompanies each
new unit. Do not substitute water or paint solvent for Piston
Lube. Ordinary oil may contaminate the paint material and is not
recommended.
If the paint pump has been out of service for an extended period
of time, it may be necessary to prime the suction by pouring
some of the paint solvent into the inlet siphon tube to restart. It
is extremely important that the threads on the inlet siphon
hose coupling are properly sealed. Any air leakage will
produce erratic operation of pump and may damage the
system. The up and down strokes shoudl be approximately
equal in time. That is, one should not be faster than the other.
A fast up or down stroke may indicate air in the system or
malfunctioning valve or seats. See the Troubleshooting Guide.
Hydraulic Motor & Fluid Pump Service
See the individual Technical Data Sheets for maintenance and
service instructions on the reciprocating hydraulic motor and the
uid pump.